Case Study / Commercial Office Building
Project Overview
This case study provides insight into an energy audit project QEA Tech executed on a commercial office building complex. The study
identified preventable energy loss expenditures exceeding $150,000, and exterior defects which were responsible for Greenhouse Gas emissions amounting to 336 tCO2e.
Problem Statement
The building management was facing high energy expenditures
and failing building envelope elements and was looking for a
targeted retrofit to reduce operational costs while
minimizing capital burden.
Objectives
The objectives of the project were to:
- Identify failing building elements like windows, doors, etc.
- Identify areas of energy loss in the building envelope
- Provide recommendations for targeted retrofits
- Provide an analysis on possible energy savings and estimated payback period
Building Details
Building Type: Commercial office building
Geographical Location: Vancouver
Land Covered: 260,000 sq. ft.
Construction: Constructed in the in mid-’70s, this building was
renovated and expanded to in the late 2000s
Weather Conditions
- Warm and temperate climate
- Cold and rainy winters
- Average annual temperatures vary between 37 and 64 degrees
Pre-Operation
The QEA operations and project team conducted a pre-operation
plan after meeting the property manager. The plan consisted of:
- Pre-operations questionnaire filled out by the property manager
- Sharing details about the building envelope and equipment
- Areas of interest requiring special attention specified by building operations team
- Flight plan created by the drone operations team used for the drone flights and thermographic scans
- Operations scheduling done with the property manager to align on the date and time for the scans
Operation
QEA Tech team started the operation preparation phase at 10:40
p.m. on January 26, 2022, for the complete aerial thermography
inspection of the building. The operation started at 11:00 p.m.
Aerial thermography inspections took two nights, where all
different facade elements of the building were thoroughly
scanned by industrial UAV units equipped with advanced thermal
and visual imaging systems. The 3-D scan was completed at noon
on January 28.
Through this operation, 100+ data points were captured from the
building; the most concerning areas of interest are included in
this study. These data points were analyzed through QEA Tech’s
proprietary analysis algorithms and validated by QEA Tech’s
application team.
Pre-specified areas of interest on the building were analyzed
further, and Qualitative and Quantitative Thermography Reports
were generated for such building sections.
Post-Operation
The images captured during the operation were processed by the
QEA Tech team for a qualitative and quantitative analysis in QEA
Tech proprietary patented software.
The Building Science team used the information provided by the
property manager, alongside the outputs generated by the
software, to create final reports for the client.
Key Issues
- Underperforming IGU frames and door frames (energy loss due to uninsulated fenestrations)
- Glazing units losing argon gas fill
- Unintentional vegetation on the roof leading to moisture accumulation and mold formation
- Thermal bridging (energy loss due to uninsulated connection between building elements)
Thermal Imagery
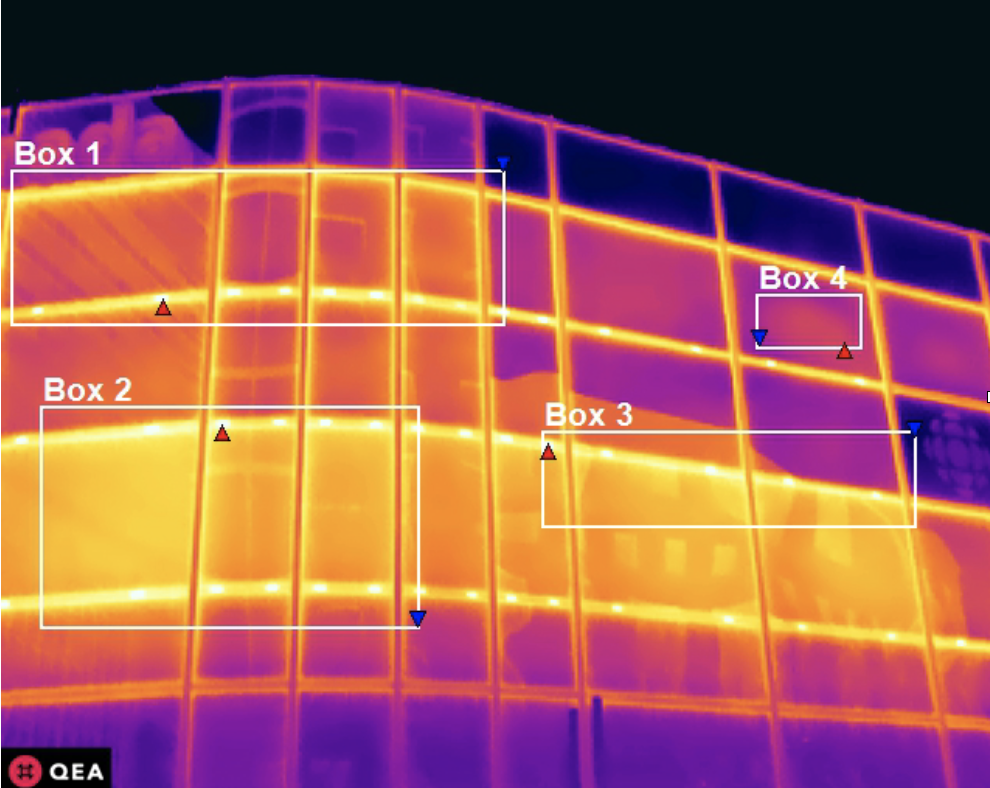
The image shows a portion of a façade of the building where the
thermal behavior of various types of energy loss can be detected.
- Box 1, 2 and 3 displays signs of heat loss through the window frames. Window frames can be made from various materials offering different levels of performance and insulation values Window assemblies should be replaced with thermally broken durable windows to decrease heat loss.
- Box 4 shows an insulated glass unit that has partially or entirely lost its insulation gas, which causes energy loss through the window. Argon gas can be replaced depending on now much the gas level has fallen and the extent of the damage
Key Findings
The average U-Values of building elements compares to building
code as follows:
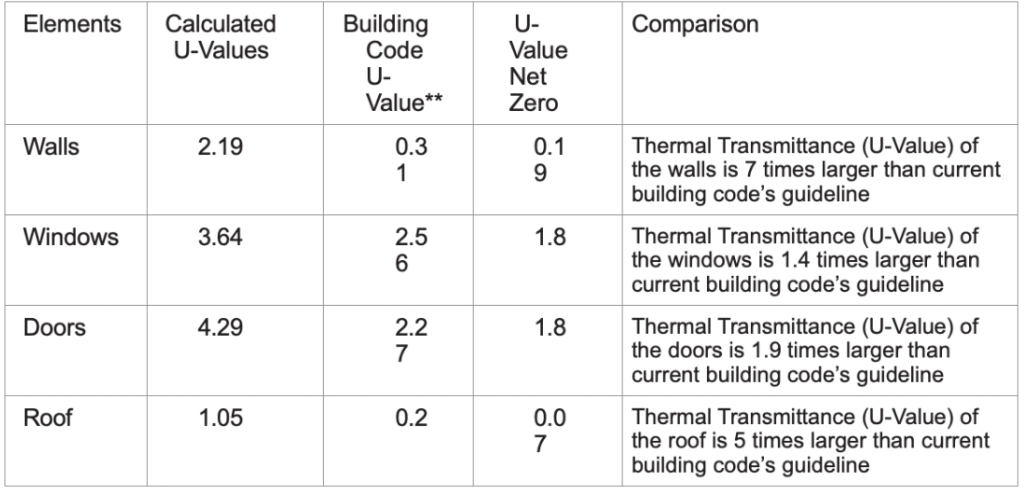
The building is losing approximately 2,884 MWh of generating
heating and cooling energy through the building envelope every
year. If brought up to code, these losses could be reduced by
1,977 MWh.
Recommendations
- Fix/upgrade roof to prevent moisture accumulation and vegetation
- Add additional layer of insulation where applicable
- Add argon gas to, or replace IGUs, where applicable
- Post-retrofit thermal scan to verify building performance
Preventable Energy Loss
At equivalent kW cost ($Kew) of $0.08/kWh, these losses translate
to a total expenditure of $230,646 with $158,153 of this amount
being preventable.